Indy Car Engines: Evolution and Performance Specifications for 2025 Season
IndyCar engines represent some of the most impressive engineering in motorsport today. These power units have evolved significantly over the years. The current generation features 2.2-liter twin-turbocharged V6 engines that produce around 700 horsepower.
IndyCar is currently transitioning to a new hybrid power unit system. This system will combine the traditional internal combustion engine with electric power components for improved performance and efficiency.
The engines are supplied by just two manufacturers – Chevrolet and Honda – creating a competitive but controlled environment. Each IndyCar team is limited to four engines per season. Grid penalties are enforced if they exceed this allocation. This restriction creates an interesting balance between pushing for maximum performance and maintaining reliability throughout the grueling schedule.
What makes these engines particularly impressive is their versatility. They must perform on oval superspeedways exceeding 230 mph, technical road courses, and tight street circuits – all with the same basic configuration. The upcoming hybrid technology will add another dimension to this challenge when it debuts in the 2024 season, pushing IndyCar engineering into exciting new territory.
History of Indy Car Engines
Contents
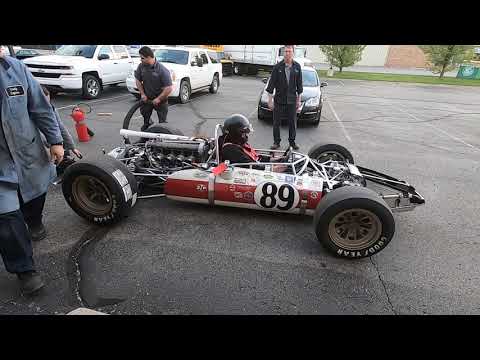
The evolution of IndyCar engines represents one of motorsport’s most fascinating technological journeys, marked by innovative designs and fierce competition among manufacturers seeking the perfect balance of power, reliability, and efficiency.
Early Innovations and Dominant Engines
The most legendary engine in Indianapolis 500 history was undoubtedly the Offenhauser, affectionately known as the “Offy.” This powerplant dominated the Brickyard for decades, securing an astounding twenty-seven Indy 500 victories.
Ford made its dramatic entrance into IndyCar racing in the 1960s. The Ford 255 cid V8 engine, developed with British engineering firm Cosworth, challenged Offy’s dominance. This partnership created formidable competition for the aging Offenhauser design.
The early era was characterized by four-cylinder engines gradually giving way to more powerful V8 configurations. Engine builders like Leo Goossen and Bud Winfield created innovative designs that pushed the boundaries of performance.
Reliability was as crucial as raw power. Many brilliant engines failed to complete the grueling 500-mile distance, making durability engineering equally important to horsepower figures.
The Turbocharged Era
Turbocharging revolutionized IndyCar racing, completely transforming performance capabilities. The technology allowed smaller displacement engines to produce massive power figures through forced induction.
By the 1970s, turbo engines became the standard in top-level American open-wheel racing. The Cosworth DFV, originally designed for Formula 1, was adapted with turbocharging for IndyCar competition and became highly successful.
After the CART/IRL split in the 1990s, engine regulations diverged. CART continued with 2.65L turbo V8s running on methanol, while the IRL initially opted for 4.0L naturally-aspirated V8s before later downsizing to 3.5L.
Turbo boost pressure became a critical variable in race strategy. Teams could dial up additional power for qualifying or crucial race moments at the cost of increased fuel consumption and engine stress.
Modern Developments
Today’s NTT IndyCar Series features a battle between Honda and Chevrolet with remarkably similar specifications. Both manufacturers supply twin-turbocharged V-6 engines limited to 10,300 rpm, producing approximately 650 horsepower.
The modern era introduced the “push-to-pass” system, giving drivers temporary power boosts for overtaking. This tactical element adds an extra dimension to racing strategy beyond raw engine performance.
Looking toward the future, IndyCar is developing hybrid technology to complement the internal combustion engines. This system will utilize regenerative braking to store energy, which can then be deployed for additional power during races.
Fuel efficiency has become increasingly important in modern IndyCar engines. The competition between Honda and Chevrolet extends beyond raw power to include fuel economy and power delivery characteristics that suit different tracks and driving styles.
Technical Specifications

IndyCar engines are precision-engineered marvels that blend power, efficiency, and reliability to handle the extreme demands of high-speed racing. These compact powerplants deliver remarkable performance while adhering to strict technical regulations.
Engine Design
The heart of every IndyCar is a 2.2-liter, twin-turbocharged V-6 engine that showcases cutting-edge racing technology. Unlike older race engines that used V8 configurations, modern IndyCar engines utilize a V-6 layout with Dual Overhead Cam (DOHC) valve trains.
Both engine suppliers—Chevrolet and Honda—build their power units with aluminum cylinder heads and blocks to minimize weight. The architecture features dual overhead cams with four valves per cylinder, maximizing airflow efficiency and combustion.
These engines are designed to withstand the tremendous stresses of events like the Indy 500, where reliability is as crucial as raw power. Engineers focus on optimizing every component, from cylinder head design to internal friction reduction.
Performance Metrics
IndyCar engines produce astonishing power from relatively small displacement. They generate approximately 550-700 horsepower, with output varying based on the turbo boost pressure settings for different track types.
The rev limit is equally impressive, with engines capable of reaching 12,000 RPM during normal operation and up to 12,200 RPM when using the push-to-pass overtake feature. This high-revving capability helps deliver responsive power throughout the racing speed range.
Torque figures are less publicized than horsepower, but these engines produce substantial torque—around 350 lb-ft—delivered across a broad RPM band to provide excellent drivability out of corners.
Key Performance Numbers:
- Displacement: 2.2 liters
- Horsepower: 550-700 HP (track dependent)
- Max RPM: 12,000 standard / 12,200 overtake
- Weight: Approximately 350 lbs
Fuel and Intake Systems
IndyCar engines utilize a specialized Speedway E85 fuel, which contains 85 percent ethanol and 15 percent gasoline. This renewable fuel blend offers both environmental benefits and performance advantages for high-compression racing engines.
The intake systems feature sophisticated twin-turbochargers that force compressed air into the engine, dramatically increasing power output. Boost pressure is regulated by series officials depending on the track type—lower for ovals like the Indy 500 and higher for road courses.
Complex intake manifold designs optimize airflow to each cylinder, with engineers constantly refining these systems to extract maximum performance. Fuel delivery is handled by precision direct injection systems that meter fuel with extraordinary accuracy.
Air-fuel ratios are continuously monitored and adjusted throughout races to balance maximum power with fuel efficiency—a critical factor in race strategy where saving a pit stop can mean the difference between winning and losing.
Engine Components and Materials

IndyCar engines rely on high-performance materials and precision-engineered components to deliver exceptional power and reliability under extreme conditions. These purpose-built racing powerplants represent the cutting edge of motorsport technology.
Crankshaft and Connecting Rods
The crankshaft forms the backbone of every IndyCar engine. Teams like Team Penske rely on forged steel crankshafts that offer superior strength-to-weight ratios compared to cast alternatives. These components must withstand incredible forces while rotating at speeds exceeding 12,000 RPM.
Connecting rods in IndyCar engines are typically manufactured from titanium alloys or specialized steel. These components transfer power from the pistons to the crankshaft while enduring tremendous stress cycles.
The manufacturing tolerances are incredibly tight—measured in microns rather than millimeters. This precision ensures optimal balance and reduces vibration, critical for extracting maximum performance from the Dallara IR-12 chassis.
Most modern IndyCar engines feature lightweight pistons made from aluminum alloys with special coatings to reduce friction and heat transfer.
Cooling and Oiling
The cooling system in an IndyCar engine is a marvel of engineering efficiency. Unlike street cars, IndyCars utilize compact water pumps that circulate coolant through minimalist radiator systems designed to maintain optimal operating temperatures.
The oiling system employs a dry-sump configuration with external reservoirs rather than traditional oil pans. This design prevents oil starvation during high-G cornering and reduces the engine’s center of gravity.
Oil pumps in these racing engines circulate specialized synthetic lubricants through precision-machined galleries and passages. These oils contain additives that enhance protection under extreme heat and pressure conditions.
Cooling efficiency is further enhanced through the use of specialized materials in the engine block and heads. Modern IndyCar engines utilize aluminum alloys with specific heat treatment processes to optimize strength and thermal conductivity.
Teams and Manufacturers
The engine suppliers and racing teams form the backbone of IndyCar competition, creating crucial partnerships that drive technological innovation and on-track performance. These relationships have evolved significantly throughout the sport’s history, with various manufacturers entering and exiting the series.
Historical Manufacturers
IndyCar’s engine history is rich with legendary names that shaped American open-wheel racing. Offenhauser engines dominated for decades, powering vehicles to Indianapolis 500 victories from the 1930s through the 1970s. These four-cylinder powerplants became synonymous with American racing excellence.
Ford made significant contributions, particularly with their famous DFX engine developed with Cosworth that dominated the 1980s. This partnership revolutionized turbocharging technology in IndyCar racing.
A.J. Foyt found success both as a driver and team owner, working with various engine suppliers throughout his career. His influence extended beyond driving to engine development relationships.
Other notable historical suppliers included Brayton Engineering and Judd, who provided alternatives during competitive eras. Gibson Technology also contributed engine designs that influenced racing development.
Current Engine Suppliers
Today’s IndyCar field is powered by just two manufacturers: Chevrolet and Honda. Both produce 2.2-liter twin-turbocharged V6 engines that deliver approximately 700 horsepower.
These manufacturers work closely with top teams like Team Penske (Chevrolet) and Chip Ganassi Racing (Honda) to refine performance.
The current engine formula will remain in place through 2026.
The series has been actively seeking a third manufacturer to join the competition. According to recent discussions, IndyCar officials have started preliminary talks about the 2027 engine formula to attract new suppliers.
For the 2025 season, major teams include A.J. Foyt Enterprises, Andretti Global, Arrow McLaren, and Chip Ganassi Racing, each paired with either Chevrolet or Honda power.
Regulations and Innovations
IndyCar engines represent a fascinating blend of cutting-edge technology and strict regulatory oversight. The series balances performance with safety while pushing automotive innovation forward through carefully crafted technical guidelines.
Technical Regulations
The IndyCar Series has evolved its engine regulations significantly over time. Currently, teams use 2.2-liter, twin-turbocharged V-6 engines, but change is coming.
Beginning in 2022, IndyCar planned to introduce a hybrid power unit developed collaboratively with manufacturers Chevrolet (Ilmor) and Honda Performance Development.
This represents a major shift in IndyCar’s technical philosophy. The series originally announced plans for a 2.4-liter twin-turbo V6 that would produce over 900 horsepower, marking a substantial power increase.
The new regulations are designed to last six years (2022-2027), providing teams and manufacturers stability for planning and development. This long-term approach helps attract manufacturer participation while controlling costs.
Push-to-Pass System
The Push-to-Pass system represents one of IndyCar’s most exciting technical innovations. This driver-activated feature temporarily increases engine power during races, creating more overtaking opportunities and enhancing competition.
With the introduction of hybrid technology, the Push-to-Pass system is getting a significant upgrade. Drivers will now have access to more than 900 horsepower when activating the system, drawing additional power from the energy recovery system.
The hybrid implementation includes a single-source hybrid system that works alongside the internal combustion engine. This technology captures energy during braking that would otherwise be wasted as heat, storing it for later use during acceleration or overtaking maneuvers.
IndyCar officials meticulously control Push-to-Pass usage, limiting both the total activation time and frequency per race to maintain competitive balance.
Racing Events and Success
IndyCar engines have powered some of the most spectacular moments in motorsport history, delivering memorable victories across iconic American racetracks and international venues. The performance of these powerplants has directly influenced race outcomes and championship titles throughout the decades.
Iconic Races
The Indianapolis 500 stands as the crown jewel of IndyCar racing, where engines face their ultimate test over 500 grueling miles. The 2.5-mile oval at Indianapolis Motor Speedway demands both raw power and remarkable durability, with engines pushed to their absolute limits for over three hours.
The Firestone Grand Prix of St. Petersburg offers a completely different challenge – a street circuit where throttle response and drivability become crucial engine attributes. Here, the 2.2L twin-turbocharged V6 engines must deliver precise power in tight corners.
International events have also showcased IndyCar engine prowess. Several IndyCar engine manufacturers have adapted their racing technology for Le Mans competition, while the engineering principles have influenced Formula 1 powerplants.
Notable Achievements
The Chevy 2.2L twin-turbocharged V6 has dominated recent IndyCar seasons, powering multiple champions including Will Power to victory. These engines generate approximately 700 horsepower while maintaining remarkable fuel efficiency under racing conditions.
A.J. Foyt’s championship runs were powered by various engines throughout his storied career, demonstrating how driver skill combined with superior powerplants creates racing legends. More recently, Alexander Rossi’s stunning 2016 Indy 500 victory showcased how strategic engine management can overcome raw horsepower advantages.
Arrow McLaren’s recent partnership with Chevrolet represents the continuation of racing technology transfer between Formula 1 and IndyCar. Their engine development program has roots in Detroit’s automotive engineering excellence.
The evolution from methanol-fueled 4.0L V8 engines to today’s smaller displacement turbocharged units demonstrates how motorsport remains at the cutting edge of efficiency and performance.
Impact on the Automotive Industry
IndyCar engines have shaped car technology far beyond the racetrack, influencing how everyday vehicles perform and innovate. Racing has always been a testbed for new ideas that eventually make their way to consumer vehicles.
Technological Advancements
The Indianapolis 500 has served as an incubator for countless automotive innovations. Perhaps most notably, the Offenhauser engine (nicknamed “Offy”) helped pioneer turbocharging technology for gasoline engines, taking it from an experimental concept to a mainstream feature in road cars.
Today’s hybrid systems represent the next frontier. While IndyCar has faced challenges implementing its hybrid technology due to parts shortages and production lead times, the development process itself drives innovation.
Cosworth, a legendary name in racing engines, has transferred countless lessons from IndyCar to production vehicles. Their expertise in engine management systems has improved efficiency and performance in consumer cars worldwide.
Engineering and Design Influence
IndyCar’s relentless pursuit of performance has revolutionized how road cars are designed and built. The extensive use of electronics in modern IndyCars shapes consumer vehicles too. For example, engine management systems and data acquisition techniques flow from track to street.
Turbocharged engines, now commonplace in everything from economy cars to luxury vehicles, owe much of their development to racing innovations. The extreme conditions of motorsport force engineers to solve problems that eventually benefit everyday drivers.
Manufacturers like Honda and Chevrolet collaborate with IndyCar and have created a two-way street of knowledge. While these partnerships occasionally face challenges, such as the delayed implementation of new engine specifications, they remain crucial for automotive progress.